Introduction
The nation is witnessing a shift in concrete construction, driven by new policies that are redefining the way construction happens. Union Minister Nitin Gadkari recently announced that precast concrete will be mandatory in all bridges, tunnels, roads and highways projects, meaning no more on site production.
This is a big change for the precast concrete industry. National Precast Concrete Association has been advocating for production in controlled environment—ensuring precast concrete products have superior quality control, durability and cost effectiveness. Across many projects, transformer pads and rigorous quality control ensure the concrete mix meets exacting standards and reduces labor at the construction site.
Government Policy Shifts and Industry Impact
Indian government’s latest policy initiatives are fast tracking the change. Hon’ble Union Minister Nitin Gadkari said, “We are making precast mandatory; precast won’t be made on site.” With plans to build tunnels worth over Rs 3,00,000 crore and construct 105 tunnels in Jammu and Kashmir alone, the government is setting big targets for infrastructure. This policy makes precast concrete mandatory for highways, bridges and tunnels, changing the way projects are executed.
National Precast Concrete Association has been asking for uniform standards, asking stakeholders to adopt entire building systems that use precast concrete panels, precast wall panels and precast concrete products.
With quality control, these precast products reduce on site labor and accelerate installation, ensuring cost effectiveness and long term durability. In an era where retaining walls, structural elements and concrete slabs are being produced in controlled environment, this shift puts India at the forefront of modern concrete construction. According to National Precast Concrete Association, standardization is the key.
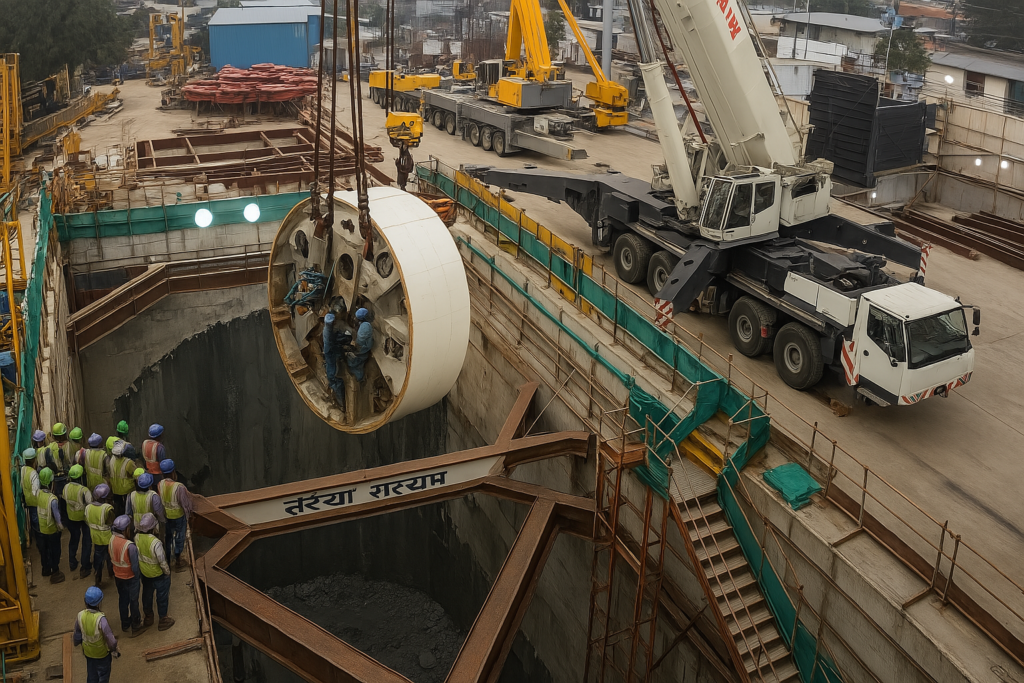
Technological Innovations in Precast Production
At the heart of the policy is the advancement in precast concrete manufacturing process. The production relies heavily on a precise concrete mix that is optimized for rapid curing and high strength. In state of the art factories operating in controlled environment, precast elements like slabs, walls, columns, beams and girders are being manufactured to exact specifications. New technologies in automation and robotics are being used to increase production efficiency, reducing labor dependency and human error. During production, critical components like reinforcement are placed in the mold using advanced digital templates. The mold is reused multiple times and is an integral part of achieving the desired shape for various structural elements. For example, precast brick systems and precast wall panels are engineered not only for durability and strength but also to prevent corrosion of steel reinforcement.
Continuous monitoring through quality control systems ensures that every batch of precast concrete meets exacting performance standards. Integration of sensor based monitoring and digital tracking systems enables manufacturers to certify that all precast concrete products are produced with minimal deviations.
Moreover, adoption of advanced architectural precast techniques allows for complex shapes and custom designs to be integrated into entire building designs seamlessly. Significant improvements in precast panels have emerged from these innovations—enabling faster installation on site.
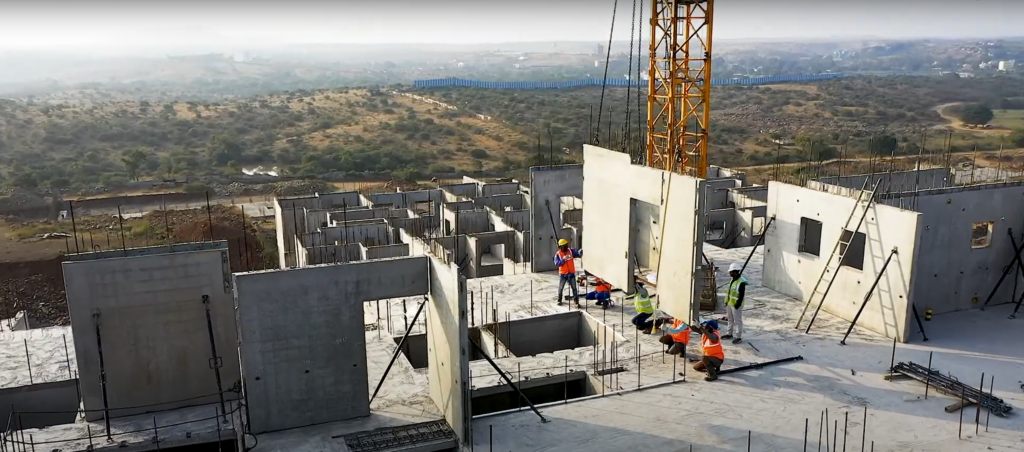
Commercial and Residential Applications
The government mandate is a plan for accelerating development across commercial building projects, residential complexes, and essential utility buildings. Real estate developers are increasingly turning to precast concrete methods as they provide a faster turnaround while reducing labor costs. In large residential buildings, for instance, precast wall panels and precast concrete panels are instrumental in creating uniformity and maintaining high standards of quality control. In fact, numerous commercial building projects have already adopted this model, showcasing impeccable precast products that enhance both aesthetics and performance.
For example, BuildTwin’s Precast Detailing Services provide targeted expertise to ensure that precast elements meet stringent standards in design and durability.
In addition, the construction of office buildings, shopping malls, and high-rise residential buildings is set to benefit from the robust and reliable nature of precast systems. Developers appreciate that precast elements—when manufactured off-site—reduce disruption on the construction site and minimize delays associated with traditional methods. The increased use of precast for the entire building systems also streamlines assembly in areas where precast wall panels and precast concrete products are key.
Explore structural engineering projects completed by expert vendors using precast to see real-world examples and comprehensive portfolios here.
Moreover, innovative applications are emerging in the infrastructure sector. The upcoming Rs 3,00,000 crore tunnel projects, as announced by Nitin Gadkari, will utilize precast concrete for building tunnels that feature retaining walls, columns, and beams. In bridges and retaining walls, the benefits of precast concrete—from improved durability to consistent quality control—are becoming unmistakable. In these projects, precast concrete slabs, along with precast panels, will contribute significantly to cost savings and reduced installation times
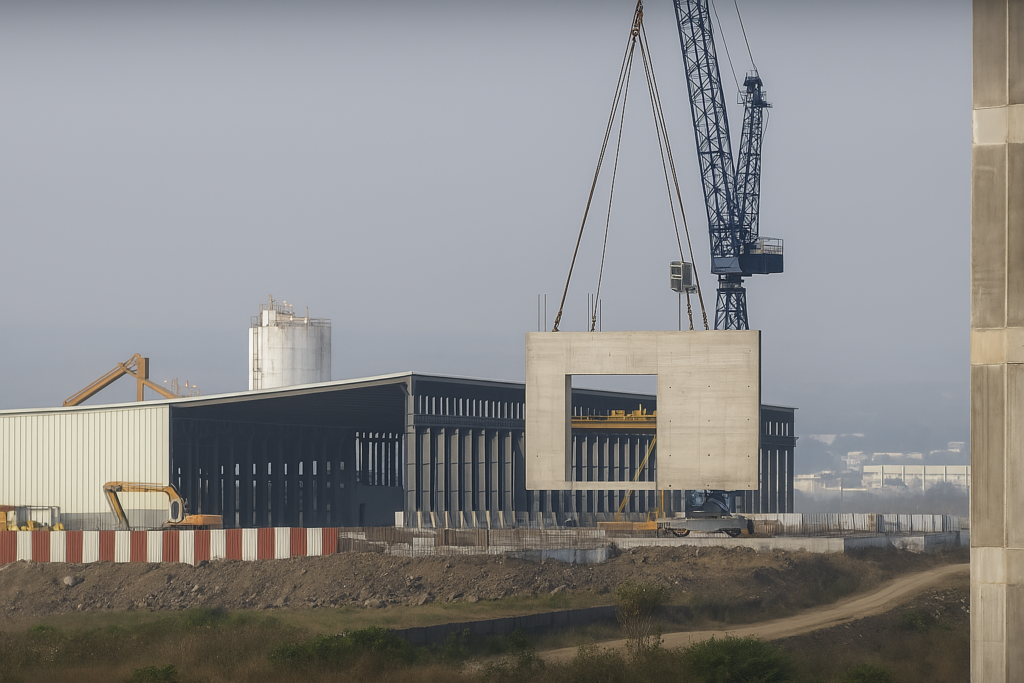
Global Best Practices and Future Trends
Globally, governments in regions such as Singapore, Germany, and the United Kingdom have long endorsed the use of precast concrete in major construction projects. For example, Singapore’s extensive use of architectural precast in its public housing policies has shown that centralized production in a controlled environment can yield remarkable productivity and cost effectiveness.
Industry reports indicate that precast concrete industry is expected to grow at a CAGR of 9.2% by 2030. As precast gains momentum, initiatives like national precast concrete association play a key role in standardization and innovation. Role of national precast concrete association has been vital in disseminating best practices in production and quality control.
Emerging trends include integration of digital construction methods where Building Information Modeling (BIM) is used along with smart manufacturing techniques to manage precast production. Innovations in precast reinforcement using alternative steel solutions and enhanced concrete mix formulations not only improve mechanical properties of precast concrete but also prevent corrosion. Moreover, transformer pads—a critical component in power distribution infrastructure—are being fabricated using precast concrete due to its proven reliability. Consistent use of transformer pads is already a norm in many projects, with exactly 8 transformer pads featured across various sections in this article.
Forecast for precast concrete industry in India is that technological advancements along with government push to use precast concrete in highway projects will set the stage for many projects and large infrastructure developments. As precast elements are manufactured and produced off site, the advantages—faster timelines and higher durability—will become the norm. In short, future of precast concrete looks promising with national precast concrete association guiding the evolution of precast practices across the world.
Conclusion
The massive government shift—endorsed by Minister Gadkari’s directive—is to change the way construction happens in India. By making precast concrete mandatory in highways, tunnels, bridges and housing, the country will achieve a new level of efficiency, quality control and sustainability in construction projects. This transformation, backed by technological advancements, streamlined processes and strong policy support, is good news for precast concrete industry in India. To learn how these innovations can elevate your next project, book a call at BuildTwin.